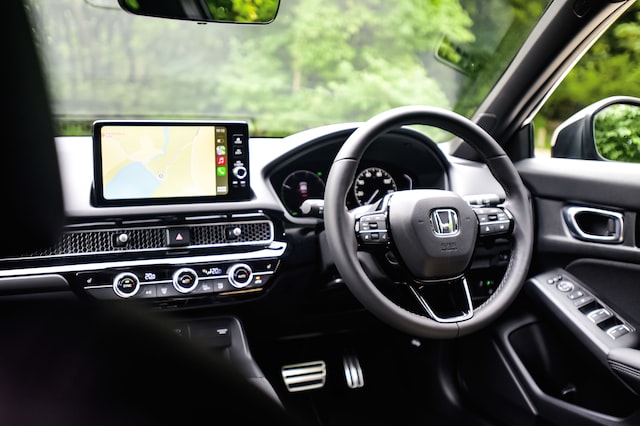
Cargroot is reader-supported. When you buy through links on our site, we may earn an affiliate commission.
Vehicles today are becoming increasingly complex with more onboard computers running the show. Therefore, car manufacturers need a way to read and diagnose any issues occurring within the vehicle’s system. This is where KWP2000 comes in!
So, what is KWP2000? Let’s find out!
What Does The Code KWP2000 Mean For Vehicles?
KWP2000 is a communication protocol that allows for efficient data exchange between a diagnostic tool such as a code scanner and electronic control units (ECUs) located inside a vehicle.
It also helps to standardize communication so that different cars from different manufacturers can talk to each other.
KWP2000 actually stands for Keyword Protocol 2000 and is part of the automotive industry’s OBD-II On-board Diagnostic System which works in unison with Diagnostic Trouble Codes (DTCs).
Together, these two systems allow auto technicians to quickly identify faults or issues in a car’s or truck’s engine without needing hours of manual testing or looking through hundreds of pages of schematics.
The code KWP2000 was adopted by automakers as early as 1998 and has since become a bridge between the vehicle and its onboard computer network.
Using this protocol enables efficient data transactions over established communications protocols like UART, CANbus, J1850VPW, etc., which makes it easier for technicians to diagnose and repair issues.
The KWP2000 protocol can be used to determine what errors have been found by reading DTC error codes that are stored when an issue occurs. This is then translated into parametric information that can identify what system within the vehicle is affected and provide further details on why it failed.
The use of Keyword Protocol 2000 significantly helps reduce diagnostics time by allowing fast adoption of new ECU variants across various manufacturers while still keeping widely accepted standards intact.
It has helped contribute to the increased level of safety that modern vehicles enjoy due to quicker response times when errors occur – errors can be pinpointed faster than ever before ensuring drivers stay safe while out on roads amidst all kinds of hazardous conditions they might encounter while driving around town or even off-roading!
What Is UDS Protocol Mean In Vehicles?
UDS protocol has been developed to improve automotive diagnostic messaging. This protocol simplifies communication by standardizing the messages used between incompatible systems (client-server communication).
In this way, it eliminates the need for custom software or hardware to communicate with each other when diagnosing errors in vehicles. It also provides a means of robustness, as the communications are less likely to be corrupted or misinterpreted due to interference from outside sources.
The UDS protocol enables further efficiency in automotive servicing and repair. By facilitating standardized digital communication with vehicle engines (ECUs), UDS allows service technicians and mechanics to efficiently diagnose multiple issues simultaneously and quickly develop strategies for quick repairs.
This is especially useful when dealing with complex problems connected with vehicular electronics such as CAN buses and ABS systems.
Additionally, UDS can be used to access real-time performance data stored within a vehicle’s ECUs: which parameters might otherwise require manual data loggers or direct measurement.
UDS makes use of two lower-level protocols – KWP2000 (ISO14230-3) and DoCAN (ISO 15765-4). KWP2000 is typically used for general engine control functions such as setting fuel injection timing or sensor readings, whereas DoCAN is well suited for handling actuator controls such as transmission shifting/braking or power steering assist/steering assist angle settings.
These protocols rely on dedicated connections that allow service facilities to control numerous parameters without having to manually make any adjustments themselves – saving time and ensuring accuracy in the diagnostics process.
Additionally, through its secure connection procedure, UDS reduces the chance that malicious agents will gain access to the vehicle’s network bus.
A Detailed Comparison Between KWP 2000 and UDS Protocol
Understanding the difference between the KWP 2000 and UDS protocol is essential for anyone looking to work in the automotive diagnostics industry. This section will provide a detailed comparison of these two protocols:
Support for In-Vehicle Communication Networks:
KWP 2000 is an older diagnostic protocol that only supports CAN (Controller Area Network) and K-line bus systems. On the other hand, UDS protocol is designed to be independent of underlying vehicle networks as it can support a wide range of buses including CAN FD (Flexible Data Rate), Local Interconnect Network (LIN), FlexRay, etc.
KWP 2000 is an older diagnostic protocol that only supports CAN (Controller Area Network) and K-line bus systems.
On the other hand, UDS protocol is designed to be independent of underlying vehicle networks. This is because it can support a wide range of buses including CAN FD (Flexible Data Rate), Local Interconnect Network (LIN), FlexRay, etc.
Transferring Key Measurement Values:
Both protocols allow for the exchange of request and command messages from test equipment to the ECU and key measurement values (data) sent back from the transmitted device in response to these requests/commands.
But there is an important difference between how this data is exchanged by each standard i.e., UDS uses two-byte long data identifiers called DIDs while KWP relies on single-byte record local identifiers along with a two-byte common identifier.
This limits its efficiency slightly compared to UDS protocol when transferring numerous measurement values at once because of its longer 2-bytes (16-bit long) identifiers compared to the 8-bit length record Local Identifier used by KWP 2000 standard.
Communication Style
The most obvious difference between the two protocols is their communication style. KWP2000 uses a symmetrical communication sequence, while UDS is event-driven and periodic.
In a KWP2000 protocol, the test equipment sends requests for information from the automotive ECU, and the ECU responds with a response message which contains data related to the request.
With UDS, however, the test equipment can send periodic requests for updated information from automotive ECUs. This can be beneficial for monitoring vital functions more closely in regular intervals, as well as detecting any deviations in vehicle conditions compared to ideal values.
Message Size
Lastly, there is also a difference in terms of message size which determines how much data each protocol transfers per transaction.
For example, a standard KWP2000 request will generally contain around 8 bytes of data while responses may have up to 154 bytes according to ISO 14230-1 specification on some systems like GM’s OBD2 implementation by General Motors since 1996 (and even earlier).
On the other hand, a normal UDS request may include up to 1460 bytes of the payload within one message due to its longer addressable length and higher data rate capabilities mentioned above.
This bodes well for transmitting larger files such as SAE J1939 or CANOpen profiles over mediums like USB/Bluetooth or LAN networks rather than via Serial buses alone which contain limited amounts of memory compared to newer incarnations of microcontrollers now equipped with 32 Megabytes (or more) RAM & Flash capacity common on today’s auto modules produced since 2013+.
Read DTC Subfunctions:
The KWP2000 protocol is an ISO 14230-4 based protocol developed in 1997 with the goal of replacing older protocols such as ISO 9141 and SAE J1939.
It is often favored due to its fast diagnosis time and reliability. Its chief advantage over other protocols is that it uses a wake-up signal on request from the diagnostics tool which allows for a faster response time from control units in the vehicle ecosystem.
Meanwhile, UDS (Unified Diagnostic Services) was introduced by the United Nations Economic Commission for Europe in 2003 as an update to KWP2000 and as part of their standardization project on On-Board Diagnostics (OBD).
UDS comes with enhanced features such as a much larger number of “Read DVT” sub-functions compared to KWP 2000 – 21 sub-functions versus 3 in the older protocol.
This allows testers to more detailed information regarding any problem codes detected during diagnosis.
This makes problem-solving much faster and more efficient since less testing needs to be done manually. Additionally, UDS supports services like “Diagnostic Session Control” which enables fault memory analysis without clearing or deleting vehicle DTCs (diagnostic trouble codes).
Final Thought
When it comes down to it, however, both protocols are extremely important when it comes to diagnosing issues within automobiles urgently.
Despite having some differences, both protocols have come together with newer generations of automobiles so that technicians can access all available data quickly for diagnosing or troubleshooting purposes without having to choose one over the other.
Ultimately, selecting either protocol depends on what your individual needs are when it comes to using them.